


I’ve been making connectors out of hot-melt for many years, and have used release paper (shiny stuff you peel stickers off of), with good success. If you have any hope of that hot-melt sticking to the wire insulation for strain relief, well, if even a tiny bit of that silicone oil gets in there, it won’t. It’s nearly impossible to clean off, and its low viscosity and tendency to wet stuff means it gets everywhere - especially places you didn’t expect it to migrate to and really don’t want it to be. My recommendation is DO NOT USE SILICONE OIL as a release agent - or for nearly anything else, for that matter.
#Cable strain relief connector home depot how to#
People know how to do that right? Most conventional PCBs if you used a hardware store iron and leaned on it, you’d burn your way through.Īnyway right, literal roll your own plug shells, roll out a piece, wrap it around, and either mush in, smooth off and bake the whole lot, or shape it, remove carefully bake then reapply with hotsnot or that ‘poxy stuff. Again though, careful with the heat when soldering. One could I guess, press bare wires into the surface of a slab and bake those for a circuit board. Soldering to put inside it, you’d want a high temperature solder. Soldering near it, you’d want to use low temperature solder and be quick. I know hobbyists tend to ignore popcorning risk on ICs and other packaged components, but I get the feels that if you wanted to put them inside clay like this you should low bake the humidity out of them first. But one could just use bare wire, and rely on the clay to do the insulating.
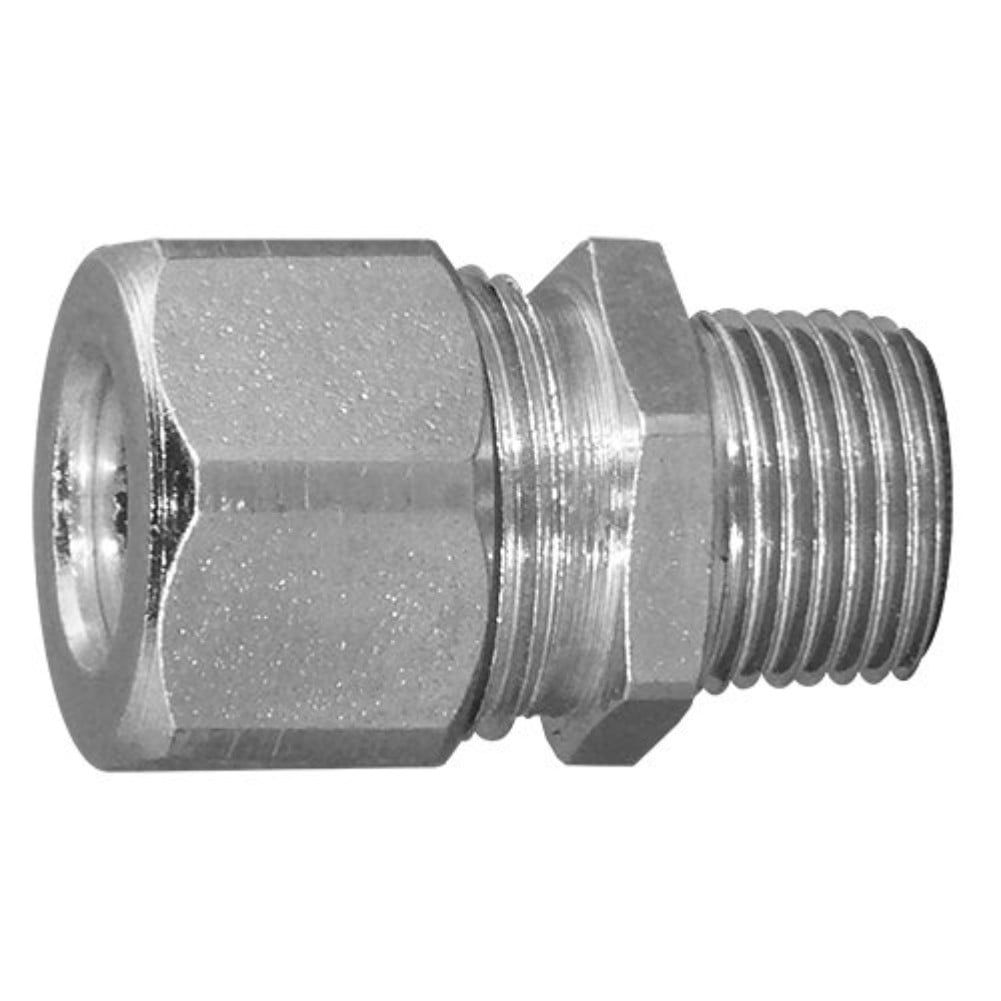
Obviously, one could encapsulate anything that will survive 135C… which means PTFE insulation on your wires (real hard to stick to btw) though I’m wondering if the old school shellacs or braided cotton would cope also. So a large amount of stuff that could be done with bakelite, we should suspect would be possible with these clays. Bakelite should ring a bell, it was pretty much the ubiquitous polymer insulator for the first 2/3 of the electrical age. Initial types were attempts to produce a replacement with non-flammable components, for Bakelite. My mind was on one set of rails yesterday evening, but now it’s not focused on “thing to make moulds for hot stuff” let’s take a minute to think about that polymer clay and how useful it might be….Īnd cures around 135 C in the oven. Posted in 3d Printer hacks, drone hacks, how-to Tagged 3d printed, battery, casting, hot glue, JST, jst-xh, lipo, mold, rc, strain relief Post navigation You can watch a short video showing how the whole thing works, below. After all, sometimes the STL file is just not quite right and if sharing CAD files is not an option for whatever reason, providing STLs that can be more easily tweaked is a welcome courtesy. That one is provided in split parts, so that one can make a mold of an arbitrary width just by stretching the middle parts as needed, then merging them together. One last thing: among the downloads you may notice one additional model. After things cool completely, just pop apart the mold (little cutouts for a screwdriver tip make this easy) and trim any excess. The small hole in the top isn’t for filling with glue, it’s to let excess escape as the mold is closed. Next the connector is laid down on top of the glue, more glue is applied, and the top of the mold is pressed in. First coat the inside surfaces of the mold with a release agent (something like silicone oil should do the trick) and then a small amount of hot glue goes in the bottom. The 3D models aren’t particularly intuitive to look at, but an instructional video makes everything clear. says to print the mold pieces in PETG, so that they can hold up to the temperature of melted glue. His project provides molds fitted for connectors with anywhere from two to eight conductors, so just pick the appropriate one and get printing. His solution is to cast them in hot glue, with the help of 3D printed molds. Found a way to add cheap strain relief to JST-XH connectors, better known to hobby aircraft folks as the charging and balance connectors on lithium-polymer battery packs.
